Plastic extrusion for creating standardized, top-grade parts
Plastic extrusion for creating standardized, top-grade parts
Blog Article
A Comprehensive Guide to the Process and Benefits of Plastic Extrusion
In the huge world of manufacturing, plastic extrusion emerges as a necessary and highly reliable process. Translating raw plastic into constant profiles, it provides to a variety of markets with its exceptional convenience.
Comprehending the Fundamentals of Plastic Extrusion
While it may show up complicated at first glance, the procedure of plastic extrusion is basically basic. The procedure begins with the feeding of plastic material, in the kind of granules, pellets, or powders, into a warmed barrel. The shaped plastic is then cooled down, strengthened, and reduced into preferred sizes, completing the procedure.
The Technical Process of Plastic Extrusion Explained
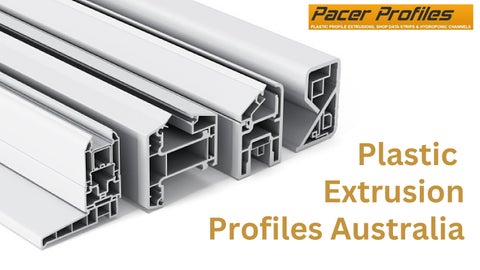
Kinds of Plastic Suitable for Extrusion
The selection of the appropriate kind of plastic is a critical aspect of the extrusion procedure. Various plastics use special homes, making them a lot more suited to specific applications. Recognizing these plastic types can substantially boost the extrusion process.
Comparing Plastic Extrusion to Other Plastic Forming Techniques
Recognizing the sorts of plastic appropriate for extrusion leads the means for a wider conversation on exactly how plastic extrusion compares to various other plastic creating techniques. These include shot molding, impact molding, and thermoforming. Each approach has its special usages and advantages. Injection molding, for instance, is outstanding for producing intricate components, while impact molding is excellent for hollow items like containers. Thermoforming excels at forming superficial or large components. Plastic extrusion is unparalleled when it comes to developing continual accounts, such as pipes, gaskets, and seals. It likewise permits a consistent cross-section along the length of the product. Hence, the selection of technique mostly depends upon the end-product requirements and specifications.
Key Benefits of Plastic Extrusion in Manufacturing
In the world of production, plastic extrusion supplies numerous substantial advantages. One notable benefit is the cost-effectiveness of the process, that makes it a financially appealing manufacturing technique. Furthermore, this method supplies superior product adaptability and boosted production speed, thus raising total manufacturing efficiency.
Cost-Effective Manufacturing Method
Plastic extrusion jumps to the forefront as an affordable production approach in production. Additionally, plastic extrusion requires less power than typical production approaches, contributing to lower operational expenses. On the whole, the monetary benefits make plastic extrusion an extremely appealing option in the production sector.
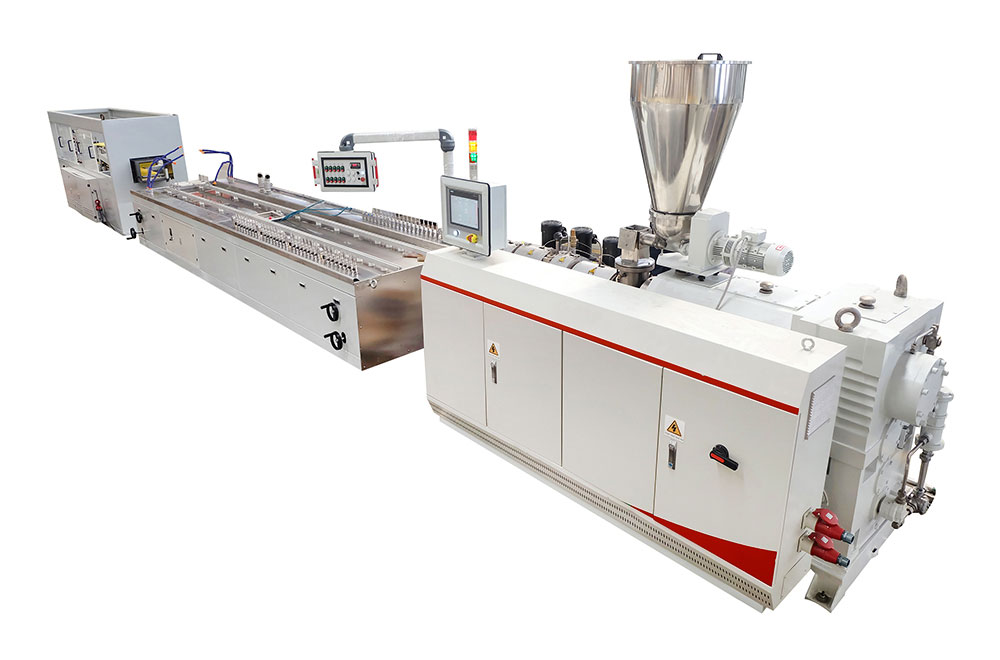
Superior Item Versatility
Beyond the cost-effectiveness of plastic extrusion, one more significant benefit in manufacturing depend on its exceptional item flexibility. This process permits the production of a large selection of products visit this website with differing sizes, layouts, and shapes, from simple plastic sheets to complex accounts. The flexibility is credited to the extrusion die, which can be customized to generate the wanted product layout. This makes plastic extrusion a suitable remedy for markets that need personalized check this plastic components, such as auto, building and construction, and packaging. The capability to produce varied products is not only beneficial in meeting specific market demands yet additionally in enabling producers to check out brand-new product lines with minimal capital expense. Fundamentally, plastic extrusion's item flexibility fosters advancement while enhancing functional efficiency.
Enhanced Manufacturing Rate
A considerable benefit of plastic extrusion exists in its improved manufacturing speed. Couple of various other manufacturing procedures can match the rate of plastic extrusion. In addition, the capability to maintain consistent high-speed manufacturing without sacrificing product quality establishes plastic extrusion apart from various other techniques.
Real-world Applications and Influences of Plastic Extrusion
In the world of manufacturing, the method of plastic extrusion holds profound significance. This procedure is commonly made use of in the manufacturing of a variety of products, such as plastic tubing, window structures, and climate stripping. Because of this, it substantially affects fields like construction, product packaging, and vehicle sectors. In addition, its effect encompasses day-to-day products, from plastic bags to toothbrushes and non reusable flatware. The economic benefit of plastic extrusion, mainly its economical and high-volume outcome, has changed production. Nevertheless, the ecological influence of plastic waste remains a problem. The industry is constantly striving for innovations in biodegradable and recyclable products, suggesting a future where the benefits of plastic extrusion can be maintained without jeopardizing ecological sustainability.
Final thought
In conclusion, plastic extrusion is a extremely efficient and reliable method of transforming raw products into varied items. It offers numerous advantages over various other plastic creating approaches, including cost-effectiveness, high outcome, minimal waste, and design flexibility. Its influence is greatly really felt in numerous markets such as building, automobile, and durable goods, making it a critical process in today's manufacturing landscape.
Digging deeper right into the technical process of plastic extrusion, it starts with the choice of the proper plastic product. Once cooled down, the plastic is from this source reduced into the needed sizes or injury onto reels if the product is a plastic film or sheet - plastic extrusion. Contrasting Plastic Extrusion to Various Other Plastic Forming Approaches
Understanding the kinds of plastic suitable for extrusion leads the means for a broader conversation on exactly how plastic extrusion stacks up versus various other plastic developing approaches. Couple of other production processes can match the speed of plastic extrusion.
Report this page